Development of new products – hemp granulate (hemp plastics)
In cooperation with the Polymer Technology College of Slovenj Gradec and Plastika Skaza d.o.o. from Velenje we were able to achieve one more important step in developing hemp composite materials – bioplastics. With new results coming in on a daily basis we can proudly state that we were able to produce the first hemp plastic composite! Putting in in different terms this means the acquisition of the first hemp composite material samples (bioplastics) and a possibility to further develop hemp products.
Mechanical properties of this hemp composite (elasticity module, tensile strength...) are by far better to comparable composites made from wood and coconut as well as being notably more age resistant. Using a Flash DSC Analysis (simulating the process of rapid heating and cooling) we have discovered a surprisingly low level of cristallization enthalpy. In other samples (wood, coconut) this level was significantly higher, as much as 5x more was observed which corellates to 5x more rapid aging of the material.
Our current mission is to ensure a sufficient ammount of fiber and their cut into agreeable size (enabling further treatment in the laboratory) until by the end of 2015 so that a greater ammount of this composite will be made.
In June 2015 hemp biogranulate was awarded as best start-up idea in national ClimateLaunchPad finals in Ljubljana which gives us even more puch for further development. Later in September 2015 we attended European Climate KIC competition in Amsterdam.
Here is a short abstract.
Hemp biogranulate is eco-friendly, fully degradable material, made from hemp fibers and lactic acid polymer (known as PLA). Both hemp and PLA are simple biodegradable and recycable materials, replacing non-degradable synthetic materials which are polluting our environment and are known to be agents of various modern day diseases.
WHY USE HEMP TO PRODUCE BIOGRANULATE?
- Hemp is easy to grow.
- Hemp provides strongest and toughest natural fiber known.
- Hemp breaths in 4x more CO2 then tree.
- Using natural resourses available locally: hemp instead of importing oil, gas...
- Having 100% biobased material, recycable, degradable, compostable
- Using agricultural bio waste (in Slovenia) to produce new, enviromental friendly material
- Replacing fossil fuel based and synthetic plastics
- Following latest EU directives and guidelines for using more recycled materials
- Stimulate local economy – grow your plastics
Hemp granulate, produced from renewable resource, sometimes even from biowaste like hemp stem is treated in Slovenia, can easily replace other thermoplastic resins which are now in common use – such as polypropylene or polystyrene resins (produced from fossil fuels). On the other hand HEMP FIBERS ARE MORE DURABLE, LIGHTER AND STRONGER. In comparison with glass fibers, hemp fibers require 10 times less energy for production and resin can be attached to hemp using less chemicals. Products from hemp fibers can be USED/REUSED SEVERAL TIMES AND/OR BE COMPOSTED AT THE END OF THEIR LIFETIME.
Identified customers are manufacturers of technical products in different industries: Automotive, Constructing, Electro, Optical, Medical, Packaging industry and any other industry with extruding or injection moulding technology.
Bottomline – what are customers benefits?
- HUGE VALUE to ECO AWARE CUSTOMERS (material is growing on the field, fibers are made out of wasted hemp stem using very little energy, zero Carbon footprint).
- RECYCABLE/COMPOSTABLE: use and reuse products.
- EXCELLENT MECHANICAL PROPERTIES: hemp bioplastics is natural composite with extremely high Tensile module (much higher when compared to other natural fibre composites (NFC) – wood or coconut fibres).
- NEW MARKET ENTRY: due to all of benefits our customers will be able to enter into new markets where new, eco-friendly, degradable, recyclable and yet durable materials are required or preffered.
- GROWING DEMANDS FOR BIOCOMPOSITES: i.e. automotive industry is required to use more recycled materials. 25% of end-of-life vehicle is considered waste and generally goes to landfills. Environmental legislation of the European Union requires the reduction of this waste to a maximum of 5% by 2015 meaning 95% of vehicle should be recycled.
- REDUCING CO2 FOOTPRINT
Cooperation with the Agricultural Institute of Slovenia to research the use of hemp hidrolate for plant protection
In March 2015 we have teamed up with the Agricultural Institute of Slovenia (KIS), namely to research hemp hidrolate.
Hidrolates are clear aqueous solution which, in addition of the essential oil derives from the destillation of the plant. They contain water-soluble compound, and even a few molecules of the essential oils of the plant. They are used in cosmetics because they are a safer and gentler alternative to the concetrated essential oil and, consequently, can relate directly to the skin.
It is speculated that due to the characteristics of hemp hidrolate, it can also be used for plant protection.
The smell of cannabis or rather the smell of essential oil is special and can have significant commercial value, wich depends on the type of cannabis. Most of the odor is not of cannabinoids (terpenofenols) but of monoterpenes and sekviterpens, which have a distinctive smell. In studies from 1980 they have identified 58 monoterpenes and 38 sekviterpens in cannabis. THC content in the essential oil is very low - below 0.08%.
Bacteriostatic activity of the essential oils have been studied already in the 80s and had reported their antifungal activity. They also studied the two compounds in the essential oil (limonene and α-pinene) and found out that they act as a repellent to many insects.
Research in the KIS will show if we can expect the similar effects with hemp hidrolate - ie anti-fungal properties and consequently its practical value in plant protection.
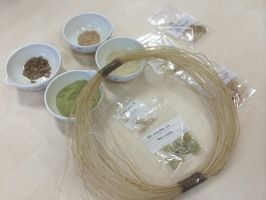
Kompozit iz konoplje
S pomočjo naprave za preoblikovanje plastičnih mas ter pripravo mešanic smo pripravili kompozit na osnovi polimlečne kisline (PLA) in konopljinih vlaken v masnem razmerju 90:10. Kot produkt smo dobili kompozitni filament (nekak neskončen špaget), ki ga lahko direktno uporabimo tudi v 3D tiskalniku in izdelamo prve vzorčne izdelke.